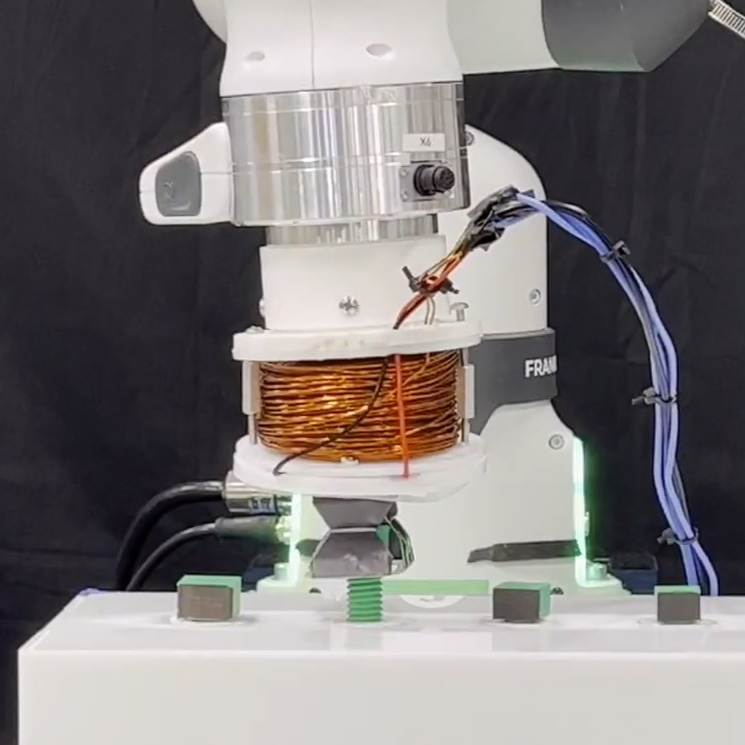 | Unger, Gabriel; Shenoy, Sridhar; Li, Tianyu; Figueroa, Nadia; Sung, Cynthia MORF: Magnetic Origami Reprogramming and Folding System for Repeatably Reconfigurable Structures with Fold Angle Control (Conference) IEEE International Conference on Robotics and Automation (ICRA), 2025. @conference{unger2025morf,
title = {MORF: Magnetic Origami Reprogramming and Folding System for Repeatably Reconfigurable Structures with Fold Angle Control},
author = {Gabriel Unger and Sridhar Shenoy and Tianyu Li and Nadia Figueroa and Cynthia Sung },
url = {https://www.youtube.com/watch?v=mUDFZ6hfgWs
https://repository.upenn.edu/entities/publication/0c5b8627-d270-455a-9a74-0bd136f28eaa
},
year = {2025},
date = {2025-05-19},
urldate = {2025-05-19},
booktitle = {IEEE International Conference on Robotics and Automation (ICRA)},
abstract = { We present the Magnetic Origami Reprogramming and Folding System (MORF), a magnetically reprogrammable system capable of precise shape control, repeated transformations, and adaptive functionality for robotic applications. Unlike current self-folding systems, which often lack re-programmability or lose rigidity after folding, MORF generates stiff structures over multiple folding cycles without degradation in performance. The ability to reconfigure and maintain structural stability is crucial for tasks such as reconfigurable tooling. The system utilizes a thermoplastic layer sandwiched within a thin magnetically responsive laminate sheet, enabling structures to self-fold in response to a combination of external magnetic field and heating. We demonstrate that the resulting folded structures can bear loads over 40 times their own weight and can undergo up to 50 cycles of repeated transformations without losing structural integrity. We showcase these strengths in a reconfigurable tool for unscrewing and screwing bolts and screws of various sizes, allowing the tool to adapt its shape to different bolt sizes while withstanding the mechanical stresses involved. This capability highlights the system’s potential for task-varying, load-bearing applications in robotics, where both versatility and durability are essential.},
keywords = {},
pubstate = {published},
tppubtype = {conference}
}
We present the Magnetic Origami Reprogramming and Folding System (MORF), a magnetically reprogrammable system capable of precise shape control, repeated transformations, and adaptive functionality for robotic applications. Unlike current self-folding systems, which often lack re-programmability or lose rigidity after folding, MORF generates stiff structures over multiple folding cycles without degradation in performance. The ability to reconfigure and maintain structural stability is crucial for tasks such as reconfigurable tooling. The system utilizes a thermoplastic layer sandwiched within a thin magnetically responsive laminate sheet, enabling structures to self-fold in response to a combination of external magnetic field and heating. We demonstrate that the resulting folded structures can bear loads over 40 times their own weight and can undergo up to 50 cycles of repeated transformations without losing structural integrity. We showcase these strengths in a reconfigurable tool for unscrewing and screwing bolts and screws of various sizes, allowing the tool to adapt its shape to different bolt sizes while withstanding the mechanical stresses involved. This capability highlights the system’s potential for task-varying, load-bearing applications in robotics, where both versatility and durability are essential. |
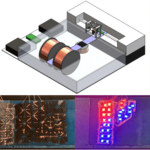 | Unger, Gabriel; Sung, Cynthia Re-programmable Matter by Folding: Magnetically Controlled Origami that Self-Folds, Self-Unfolds, and Self-Reconfigures On-Demand (Conference) 8th International Meeting on Origami in Science, Mathematics, and Education, 2024. @conference{unger2024RMBF,
title = {Re-programmable Matter by Folding: Magnetically Controlled Origami that Self-Folds, Self-Unfolds, and Self-Reconfigures On-Demand},
author = {Gabriel Unger and Cynthia Sung},
url = {https://www.youtube.com/watch?v=TuIq6ykfoOA&list=PLmM-rbrIwkWXFno8GbQYxiCcA3s8SaVJW&index=1
https://repository.upenn.edu/entities/publication/18d39cb9-f453-4cc7-9a68-47ddcc4a2924},
year = {2024},
date = {2024-07-16},
urldate = {2024-07-16},
booktitle = {8th International Meeting on Origami in Science, Mathematics, and Education},
abstract = {We present a reprogrammable matter system that changes shape in a controllable manner in real-time and on-demand. The system uses origami-inspired fabrication for self-assembly and repeated self-reconfiguration. By writing a magnetic program onto a thin laminate and applying an external magnetic field, we control the sheet to self-fold. The magnetic program can be written at millimeter resolution over hundreds of programming cycles and folding steps. We demonstrate how the same sheet can fold and unfold into multiple shapes using a fully automated program-and-fold process. Finally, we demonstrate how electronic components can be incorporated to produce functional structures such as a foldable display. The system has advantages over existing programmable matter systems in its versatility and ability to support potentially any folding sequence.},
keywords = {},
pubstate = {published},
tppubtype = {conference}
}
We present a reprogrammable matter system that changes shape in a controllable manner in real-time and on-demand. The system uses origami-inspired fabrication for self-assembly and repeated self-reconfiguration. By writing a magnetic program onto a thin laminate and applying an external magnetic field, we control the sheet to self-fold. The magnetic program can be written at millimeter resolution over hundreds of programming cycles and folding steps. We demonstrate how the same sheet can fold and unfold into multiple shapes using a fully automated program-and-fold process. Finally, we demonstrate how electronic components can be incorporated to produce functional structures such as a foldable display. The system has advantages over existing programmable matter systems in its versatility and ability to support potentially any folding sequence. |
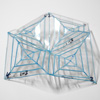 | Liu, Addison; Johnson, Mykell; Sung, Cynthia Increasing Reliability of Self-Folding of the Origami Hypar (Journal Article) In: ASME Journal of Mechanisms and Robotics, vol. 14, no. 6, pp. 061003, 2022. @article{liu2022increasing,
title = {Increasing Reliability of Self-Folding of the Origami Hypar},
author = {Addison Liu and Mykell Johnson and Cynthia Sung},
doi = {10.1115/1.4054310},
year = {2022},
date = {2022-06-01},
urldate = {2022-06-01},
journal = {ASME Journal of Mechanisms and Robotics},
volume = {14},
number = {6},
pages = {061003},
abstract = {Self-folding systems, which can transform autonomously from a flat sheet into a 3D machine, provide opportunities for rapidly fabricable robots that are deployable on-demand. Existing self-folding fabrication processes convert fold patterns into laminated structures that respond to external stimuli, most commonly heat. However, demonstrations of these approaches have been generally limited to simple fold patterns with little ambiguity in folding configuration, and the reliability of self-folding drops drastically with the fold pattern complexity. In this paper, we explore methods of biasing a symmetric fold pattern, the origami hyperbolic paraboloid (hypar), to fold into one of two possible configurations. The biasing methods are simulated using a bar-and-hinge inspired self-folding model that defines a single fold as a bending beam and the hypar crease pattern as an elastic spring network. Simulation results are also verified on physical samples. Based on these results, three techniques to bias the hypar by manipulating the target fold angles are proposed and tested. The results show that biasing a self-folding pattern can increase folding accuracy from 50% (purely random) to 70%, and provide insights for improving the reliability of future self-folding systems with complex fold patterns.},
keywords = {},
pubstate = {published},
tppubtype = {article}
}
Self-folding systems, which can transform autonomously from a flat sheet into a 3D machine, provide opportunities for rapidly fabricable robots that are deployable on-demand. Existing self-folding fabrication processes convert fold patterns into laminated structures that respond to external stimuli, most commonly heat. However, demonstrations of these approaches have been generally limited to simple fold patterns with little ambiguity in folding configuration, and the reliability of self-folding drops drastically with the fold pattern complexity. In this paper, we explore methods of biasing a symmetric fold pattern, the origami hyperbolic paraboloid (hypar), to fold into one of two possible configurations. The biasing methods are simulated using a bar-and-hinge inspired self-folding model that defines a single fold as a bending beam and the hypar crease pattern as an elastic spring network. Simulation results are also verified on physical samples. Based on these results, three techniques to bias the hypar by manipulating the target fold angles are proposed and tested. The results show that biasing a self-folding pattern can increase folding accuracy from 50% (purely random) to 70%, and provide insights for improving the reliability of future self-folding systems with complex fold patterns. |
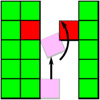 | Feshbach, Daniel; Sung, Cynthia Reconfiguring Non-Convex Holes in Pivoting Modular Cube Robots (Journal Article) In: IEEE Robotics and Automation Letters, vol. 6, no. 4, pp. 6701-6708, 2021. @article{feshbach2021reconfiguring,
title = {Reconfiguring Non-Convex Holes in Pivoting Modular Cube Robots},
author = {Daniel Feshbach and Cynthia Sung},
url = {https://repository.upenn.edu/cis_papers/865/
https://www.youtube.com/watch?v=IoyFs_K5RNE
https://github.com/SungRoboticsGroup/PIVOTING-CUBES_cube-reconfiguration},
doi = {10.1109/LRA.2021.3095030},
year = {2021},
date = {2021-07-07},
urldate = {2021-07-07},
journal = {IEEE Robotics and Automation Letters},
volume = {6},
number = {4},
pages = {6701-6708},
abstract = {We present an algorithm for self-reconfiguration of admissible 3D configurations of pivoting modular cube robots with holes of arbitrary shape and number. Cube modules move across the surface of configurations by pivoting about shared edges, enabling configurations to reshape themselves. Previous work provides a reconfiguration algorithm for admissible 3D configurations containing no non-convex holes; we improve upon this by handling arbitrary admissible 3D configurations. The key insight specifies a point in the deconstruction of layers enclosing non-convex holes at which we can pause and move inner modules out of the hole. We prove this happens early enough to maintain connectivity, but late enough to open enough room in the enclosing layer for modules to escape the hole. Our algorithm gives reconfiguration plans with O(n^2) moves for n modules.},
keywords = {},
pubstate = {published},
tppubtype = {article}
}
We present an algorithm for self-reconfiguration of admissible 3D configurations of pivoting modular cube robots with holes of arbitrary shape and number. Cube modules move across the surface of configurations by pivoting about shared edges, enabling configurations to reshape themselves. Previous work provides a reconfiguration algorithm for admissible 3D configurations containing no non-convex holes; we improve upon this by handling arbitrary admissible 3D configurations. The key insight specifies a point in the deconstruction of layers enclosing non-convex holes at which we can pause and move inner modules out of the hole. We prove this happens early enough to maintain connectivity, but late enough to open enough room in the enclosing layer for modules to escape the hole. Our algorithm gives reconfiguration plans with O(n^2) moves for n modules. |
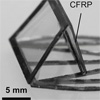 | Cha, Wujoon; Kaspar, Luke; Campbell, Matthew F.; Calenza, Thomas J.; Popov, George A.; Wang, Jeremy; Sung, Cynthia R.; Yim, Mark; Bargatin, Igor Carbon fiber–aluminum sandwich for micro-aerial vehicles and miniature robots (Journal Article) In: MRS Advances, vol. 6, pp. 477–481, 2021. @article{cha2021carbon,
title = {Carbon fiber–aluminum sandwich for micro-aerial vehicles and miniature robots},
author = {Wujoon Cha and Luke Kaspar and Matthew F. Campbell and Thomas J. Calenza and George A. Popov and Jeremy Wang and Cynthia R. Sung and Mark Yim and Igor Bargatin},
doi = {10.1557/s43580-021-00084-3},
year = {2021},
date = {2021-06-16},
urldate = {2021-06-16},
journal = {MRS Advances},
volume = {6},
pages = {477–481},
abstract = {We present carbon-fiber and aluminum sandwich plates with millimeter thicknesses that exhibit high stiffness- and strength-to-weight ratios. These composites consist of carbon-fiber-reinforced polymer faces and waterjet-cut aluminum cores, bonded using epoxy. Relative to single-ply carbon-fiber-reinforced polymer sheets, this construction provides 22-fold increases in mass-specific flexural rigidity and 18-fold increases in mass-specific flexural strength, with areal densities of only 120–260 mg/cm2. Our work represents a simple and inexpensive platform for creating extremely lightweight structural components for microflyers and small robots.},
keywords = {},
pubstate = {published},
tppubtype = {article}
}
We present carbon-fiber and aluminum sandwich plates with millimeter thicknesses that exhibit high stiffness- and strength-to-weight ratios. These composites consist of carbon-fiber-reinforced polymer faces and waterjet-cut aluminum cores, bonded using epoxy. Relative to single-ply carbon-fiber-reinforced polymer sheets, this construction provides 22-fold increases in mass-specific flexural rigidity and 18-fold increases in mass-specific flexural strength, with areal densities of only 120–260 mg/cm2. Our work represents a simple and inexpensive platform for creating extremely lightweight structural components for microflyers and small robots. |
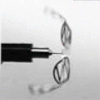 | Cha, Wujoon; Campbell, Matthew F.; Popov, George A.; Stanczak, Christopher H.; Estep, Anna K.; Steager, Edward B.; Sung, Cynthia R.; Yim, Mark H.; Bargatin, Igor Microfabricated foldable wings for centimeter-scale microflyers (Journal Article) In: Journal of Microelectromechanical Systems, vol. 29, no. 5, pp. 1127-1129, 2020. @article{cha2020microfabricated,
title = {Microfabricated foldable wings for centimeter-scale microflyers},
author = {Wujoon Cha and Matthew F. Campbell and George A. Popov and Christopher H. Stanczak and Anna K. Estep and Edward B. Steager and Cynthia R. Sung and Mark H. Yim and Igor Bargatin},
doi = {10.1109/JMEMS.2020.3013813},
year = {2020},
date = {2020-10-01},
urldate = {2020-10-01},
journal = {Journal of Microelectromechanical Systems},
volume = {29},
number = {5},
pages = {1127-1129},
abstract = {Many micro-aerial vehicles can benefit from having compact and robust pre-deployment configurations that can later transform into larger and more capable forms. We demonstrate parylene-covered silicon frames that can be folded into origami-inspired aerodynamic shapes for structural applications in centimeter-scale aircraft. By changing the spacing between the frames, we can control the conformality of the parylene deposition, which determines the directionality of the fold (mountain or valley). We fabricated a foldable propeller from such polymer-coated frames and characterized its mass and thrust.},
keywords = {},
pubstate = {published},
tppubtype = {article}
}
Many micro-aerial vehicles can benefit from having compact and robust pre-deployment configurations that can later transform into larger and more capable forms. We demonstrate parylene-covered silicon frames that can be folded into origami-inspired aerodynamic shapes for structural applications in centimeter-scale aircraft. By changing the spacing between the frames, we can control the conformality of the parylene deposition, which determines the directionality of the fold (mountain or valley). We fabricated a foldable propeller from such polymer-coated frames and characterized its mass and thrust. |
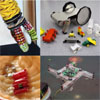 | Rus, Daniela; Sung, Cynthia Spotlight on origami robots (Journal Article) In: Science Robotics, vol. 3, no. 15, pp. eaat0938, 2018. @article{rus2018spotlight,
title = {Spotlight on origami robots},
author = {Daniela Rus and Cynthia Sung},
doi = {10.1126/scirobotics.aat0938},
year = {2018},
date = {2018-02-28},
urldate = {2018-02-28},
journal = {Science Robotics},
volume = {3},
number = {15},
pages = {eaat0938},
abstract = {Origami robots promise a future with increased customizability and adaptability in autonomous machines.},
keywords = {},
pubstate = {published},
tppubtype = {article}
}
Origami robots promise a future with increased customizability and adaptability in autonomous machines. |
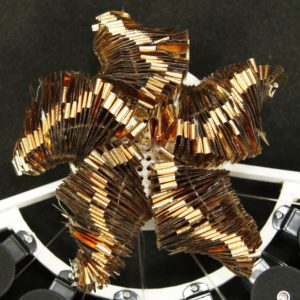 | Sung, Cynthia; Lin, Rhea; Miyashita, Shuhei; Yim, Sehyuk; Kim, Sangbae; Rus, Daniela Self-folded soft robotic structures with controllable joints (Conference) IEEE International Conference on Robotics and Automation (ICRA), 2017. @conference{sung2017self,
title = {Self-folded soft robotic structures with controllable joints},
author = {Cynthia Sung and Rhea Lin and Shuhei Miyashita and Sehyuk Yim and Sangbae Kim and Daniela Rus},
doi = {10.1109/ICRA.2017.7989072},
year = {2017},
date = {2017-05-29},
urldate = {2017-05-29},
booktitle = {IEEE International Conference on Robotics and Automation (ICRA)},
pages = {580-587},
abstract = {This paper describes additive self-folding, an origami-inspired rapid fabrication approach for creating actuatable compliant structures. Recent work in 3-D printing and other rapid fabrication processes have mostly focused on rigid objects or objects that can achieve small deformations. In contrast, soft robots often require elastic materials and large amounts of movement. Additive self-folding is a process that involves cutting slices of a 3-D object in a long strip and then pleat folding them into a likeness of the original model. The zigzag pattern for folding enables large bending movements that can be actuated and controlled. Gaps between slices in the folded model can be designed to provide larger deformations or higher shape accuracy. We advance existing planar fabrication and self-folding techniques to automate the fabrication process, enabling highly compliant structures with complex 3-D geometries to be designed and fabricated within a few hours. We describe this process in this paper and provide algorithms for converting 3-D meshes into additive self-folding designs. The designs can be rapidly instrumented for global control using magnetic fields or tendon-driven for local bending. We also describe how the resulting structures can be modeled and their responses to tendon-driven control predicted. We test our design and fabrication methods on three models (a bunny, a tuna fish, and a starfish) and demonstrate the method's potential for actuation by actuating the tuna fish and starfish models using tendons and magnetic control.},
keywords = {},
pubstate = {published},
tppubtype = {conference}
}
This paper describes additive self-folding, an origami-inspired rapid fabrication approach for creating actuatable compliant structures. Recent work in 3-D printing and other rapid fabrication processes have mostly focused on rigid objects or objects that can achieve small deformations. In contrast, soft robots often require elastic materials and large amounts of movement. Additive self-folding is a process that involves cutting slices of a 3-D object in a long strip and then pleat folding them into a likeness of the original model. The zigzag pattern for folding enables large bending movements that can be actuated and controlled. Gaps between slices in the folded model can be designed to provide larger deformations or higher shape accuracy. We advance existing planar fabrication and self-folding techniques to automate the fabrication process, enabling highly compliant structures with complex 3-D geometries to be designed and fabricated within a few hours. We describe this process in this paper and provide algorithms for converting 3-D meshes into additive self-folding designs. The designs can be rapidly instrumented for global control using magnetic fields or tendon-driven for local bending. We also describe how the resulting structures can be modeled and their responses to tendon-driven control predicted. We test our design and fabrication methods on three models (a bunny, a tuna fish, and a starfish) and demonstrate the method's potential for actuation by actuating the tuna fish and starfish models using tendons and magnetic control. |
| Sung, Cynthia; Bern, James; Romanishin, James; Rus, Daniela Reconfiguration planning for pivoting cube modular robots (Conference) IEEE International Conference on Robotics and Automation (ICRA), 2015. @conference{sung2015reconfiguration,
title = {Reconfiguration planning for pivoting cube modular robots},
author = {Cynthia Sung and James Bern and James Romanishin and Daniela Rus},
doi = {10.1109/ICRA.2015.7139451},
year = {2015},
date = {2015-05-26},
booktitle = {IEEE International Conference on Robotics and Automation (ICRA)},
pages = {1933-1940},
abstract = {In this paper, we present algorithms for self-reconfiguration of modular robots that move by pivoting. The modules are cubes that can pivot about their edges along the x̂, ŷ, or ẑ axes to move on a 3-dimensional substrate. This is a different model from prior work, which usually considers modules that slide along their faces. We analyze the pivoting cube model and give sufficient conditions for reconfiguration to be feasible. In particular, we show that if an initial configuration does not contain any of three subconfigurations, which we call rules, then it can reconfigure into a line. We provide provably correct algorithms for reconfiguration for both 2-D and 3-D systems, and we verify our algorithms via simulation on randomly generated 2-D and 3-D configurations.},
keywords = {},
pubstate = {published},
tppubtype = {conference}
}
In this paper, we present algorithms for self-reconfiguration of modular robots that move by pivoting. The modules are cubes that can pivot about their edges along the x̂, ŷ, or ẑ axes to move on a 3-dimensional substrate. This is a different model from prior work, which usually considers modules that slide along their faces. We analyze the pivoting cube model and give sufficient conditions for reconfiguration to be feasible. In particular, we show that if an initial configuration does not contain any of three subconfigurations, which we call rules, then it can reconfigure into a line. We provide provably correct algorithms for reconfiguration for both 2-D and 3-D systems, and we verify our algorithms via simulation on randomly generated 2-D and 3-D configurations. |
| Miyashita, Shuhei; Guitron, Steven; Ludersdorfer, Marvin; Sung, Cynthia; Rus, Daniela An untethered miniature origami robot that self-folds, walks, swims, and degrades (Conference) IEEE International Conference on Robotics and Automation (ICRA), IEEE, 2015. @conference{miyashita2015untethered,
title = {An untethered miniature origami robot that self-folds, walks, swims, and degrades},
author = {Shuhei Miyashita and Steven Guitron and Marvin Ludersdorfer and Cynthia Sung and Daniela Rus},
doi = {10.1109/ICRA.2015.7139386},
year = {2015},
date = {2015-05-26},
booktitle = {IEEE International Conference on Robotics and Automation (ICRA)},
pages = {1490-1496},
publisher = {IEEE},
abstract = {A miniature robotic device that can fold-up on the spot, accomplish tasks, and disappear by degradation into the environment promises a range of medical applications but has so far been a challenge in engineering. This work presents a sheet that can self-fold into a functional 3D robot, actuate immediately for untethered walking and swimming, and subsequently dissolve in liquid. The developed sheet weighs 0.31 g, spans 1.7 cm square in size, features a cubic neodymium magnet, and can be thermally activated to self-fold. Since the robot has asymmetric body balance along the sagittal axis, the robot can walk at a speed of 3.8 body-length/s being remotely controlled by an alternating external magnetic field. We further show that the robot is capable of conducting basic tasks and behaviors, including swimming, delivering/carrying blocks, climbing a slope, and digging. The developed models include an acetone-degradable version, which allows the entire robot's body to vanish in a liquid. We thus experimentally demonstrate the complete life cycle of our robot: self-folding, actuation, and degrading.},
keywords = {},
pubstate = {published},
tppubtype = {conference}
}
A miniature robotic device that can fold-up on the spot, accomplish tasks, and disappear by degradation into the environment promises a range of medical applications but has so far been a challenge in engineering. This work presents a sheet that can self-fold into a functional 3D robot, actuate immediately for untethered walking and swimming, and subsequently dissolve in liquid. The developed sheet weighs 0.31 g, spans 1.7 cm square in size, features a cubic neodymium magnet, and can be thermally activated to self-fold. Since the robot has asymmetric body balance along the sagittal axis, the robot can walk at a speed of 3.8 body-length/s being remotely controlled by an alternating external magnetic field. We further show that the robot is capable of conducting basic tasks and behaviors, including swimming, delivering/carrying blocks, climbing a slope, and digging. The developed models include an acetone-degradable version, which allows the entire robot's body to vanish in a liquid. We thus experimentally demonstrate the complete life cycle of our robot: self-folding, actuation, and degrading. |
| Miyashita, Shuhei; DiDio, Isabello; Ananthabhotla, Ishwarya; An, Byoungkwon; Sung, Cynthia; Arabagi, Slava; Rus, Daniela Folding angle regulation by curved crease design for self-assembling origami propellers (Journal Article) In: ASME Journal of Mechanisms and Robotics, vol. 7, no. 2, pp. 021013, 2015. @article{miyashita2015folding,
title = {Folding angle regulation by curved crease design for self-assembling origami propellers},
author = {Shuhei Miyashita and Isabello DiDio and Ishwarya Ananthabhotla and Byoungkwon An and Cynthia Sung and Slava Arabagi and Daniela Rus},
doi = {10.1115/1.4029548},
year = {2015},
date = {2015-02-27},
journal = {ASME Journal of Mechanisms and Robotics},
volume = {7},
number = {2},
pages = {021013},
abstract = {This paper describes a method for manufacturing complex three-dimensional curved structures by self-folding layered materials. Our main focus is to first show that the material can cope with curved crease self-folding and then to utilize the curvature to predict the folding angles. The self-folding process employs uniform heat to induce self-folding of the material and shows the successful generation of several types of propellers as a proof of concept. We further show the resulting device is functional by demonstrating its levitation in the presence of a magnetic field applied remotely.},
keywords = {},
pubstate = {published},
tppubtype = {article}
}
This paper describes a method for manufacturing complex three-dimensional curved structures by self-folding layered materials. Our main focus is to first show that the material can cope with curved crease self-folding and then to utilize the curvature to predict the folding angles. The self-folding process employs uniform heat to induce self-folding of the material and shows the successful generation of several types of propellers as a proof of concept. We further show the resulting device is functional by demonstrating its levitation in the presence of a magnetic field applied remotely. |